شمش فولادی
16 خرداد 1402
مطالعه مقاله 4 دقیقه زمان نیاز دارد
شمش فولادی که به آن شمش آهن نیز گفته می شود اولین محصول جامد و قابل حمل و نقل به دست آمده از فرایند تولید فولاد است. در واقع شمشها محصولات نیمه ساختهای هستند که در مراحل بعد تحت فرایندهای دیگر به قطعات مورد نیاز در میآیند و در اینجا فرایند شمش سازی یکی از فرایندهای میانی نورد فولادها است.
پس از استخراج آهن و تولید فولاد خام، در اثر انجماد فلز مذاب در قالب، شمش فولادی بهصورت جامد و در ابعاد قابل حمل تولید می شود.
انواع شمش فولادی و کاربردهای آن
شمش ها بر اساس ابعادشان به چهار دسته تقسیم می شوند که هر کدام کاربرد خاص خود را در صنایع تولید محصولات فولادی دارد.
برای تولید هر نوع محصول از شمش فولادی، ابتدا شمش مخصوص تولید آن محصول در کوره هایی تا دمای 900 درجه سانتیگراد حرارت می بیند تا برای تولید مقاطع و محصولات نورد گرم آماده شود.
شمش دستی (Ingot)
قطعات شمش دستی ذوزنقه شکل است و طول هر شاخه حداکثر به دو متر میرسد . دلیل حالت ذوزنقه ای سطح مقطع شمش قالبگیری دستی، راحت تر بودن خارج کردن از قالب و حمل و نقل آسان آن است این محصول معمولا در کارگاههای کوچک تولید می شود.
بیلت (Billet) یا شمشال
به شمشی که مستقیما از روش توليد ccm به مصرف نورد برسد شمش ccm يا بيلت یا شمشال گفته مى شود.
بیلت طول بیشتری نسبت به شمش دارد و با سطح مقطع دایره یا مربع با عرضی کمتر از ۱۵سانتی متر تولید میشود.
به دلیل اضلاع یکسان مربعی یا دایره ای شکل بیلت و طول بیشتری که نسبت به شمش دستی دارد بیشترین کاربرد آن در مقاطع توپر است. از بیلت در تولید میلگرد و مفتول و تسمه استفاده می شود.
از مزایای بیلت این است که هنگام استفاده از آن برای تولید مقاطع می توان آن را در مرکزی ترین قسمت قالب قرار داد بنابراین گداخته ترین بخش به مقطع مورد نظر تبدیل می شود. این کار باعث می گردد خواص مکانیکی محصول در سراسر طول تولید یکنواخت توزیع شود.
خود بیلت نیز طبق استاندارد DIN آلمان به دو دسته sp 3و sp5 تقسیم میشود که تفاوتشان در این است که بیلت sp3 انعطافپذیری بالاتری نسبت به بیلت sp5 دارد و در عوض استحکام بیلت sp5 نسبت به بیلت sp3 بیشتر است.
بلوم (Bloom) یا فابریک
بلوم که به د لیل شباهتش به ابزار بنایی شمشه در فارسی به آن شمشه نیز گفته می شود در واقع بیلتی است که طول بلندتر و سطع مقطع بزرگتری دارد. به همین دلیل بلوم برای تولید تیرآهن، ریل، سپری، ناودانی، قوطی و … کاربرد دارد از برش کناره های اسلب نیز میتوان بلوم تولید کرد.
نام جدیدی که تاجران به عنوان فابریک به کار می برند همان بلوم است .
شمش اسلب (Slab) یا تختال
اسلب یا تختال، به نوعی از شمش های فولادی گفته می شود که دارای سطح مقطع مستطیل شکل در ابعاد 1200*200 mm و یا 1200*250 mm هستند و به طول های مختلف و تا حداکثر 12 متر تولید می شوند. از این نوع شمش فولادی برای تولید انواع ورق های فولادی استفاده می گردد .
آنالیز شمش فولادی
به دلیل اینکه در تولید محصولات فولادی نهایی از شمش مانند میلگرد از کربن اسستفاده می شود، در آنالیز شمش میزان کربن موجود در آن اهمیت ویژه ای دارد. به عنوان مثال اگر بخواهیم میلگرد سایز 14 تا 40 تهیه کنیم، شمش باید با کربن 30 تا 35 باشد و برای سایزهای پایین تر، باید میزان کربن کمتر باشد تا محصول به دست آمده کشش و نرمی بیشتری داشته باشد.
شمش 125، 130 و150 برای تولید میلگرد مناسب است و در کارخانه های مدرن و به روز امکان تولید میلگرد با هر دو شمش بلوم و بیلت وجود دارد.
روش های تولید شمش فولاد
شمش فولادی با دو روش کوره القایی و قوس الکتریکی تولید می شود. هریک از این دو روش مزایا و معایبی دارد و و شمش تولید شده دارای ویژگیهایی خواهد بود که در ادامه به آن خواهیم پرداخت.
همانطور که در مطلب سنگ آهن گفته شد، سنگ آهن ماده اولیه تولید فولاد است. روش کوره الکتریکی و کوره القایی دو روش تبدیل سنگ آهن به فولاد است. که در جهان غالبا فولاد به روش کوره بلند تولید می شود اما در ایران از روش کوره الکتریکی استفاده می شود.
ابتدا سنگ آهن استخراج شده به کوره ها فرستاده می شود و سپس. در این کوره ها، پس از مرحله پیش پخت و کلوخه سازی، کک و آهک را به کوره اضافه میکنند تا آهن و چدن را از سنگ آهن جدا کنند. بعد از آن، آهن خام به فولاد مذاب تبدیل می شود. سپس ناخالصی های فولاد خام مانند کربن به میزان مختلفی به وسیله اکسیژن از آن جدا می شود تا فولاد خام به دست آید. این فولاد مذاب که به میزان مشخص شده در آنالیز، ناخالصی هایش جدا شده به واحد ریخته گری برده شده، داخل قالب ها ریخته می شود. سپس آن را بر روی غلطکی قرار می دهند و با پاشیدن آب عملیات خنک سازی انجام می شود. پس از خنک شدن انواع شمش را به طول دلخواه برش می دهند.
تولید شمش با روش کوره القایی
در روش کوره القایی ابتدا آهن قراضه را با کمک سبدهای مخصوص، داخل کوره می ریزند و هم زمان با ذوب قراضه ها، ترکیبی از آهن اسفنجی و مواد سرباره ساز مثل کک، بنتونیت، آهک، سایر مواد افزودنی از قسمت بالای کوره به ذوب افزوده می شود. بعد از نمونه گیری، دمش اکسیژن (که باعث اکسیداسیون ناخالصی ها به ویژه کربن در مذاب می شود) صورت می گیرد و بعد از آن همگن سازی است که به فولاد مذاب تبدیل می شود. در واحد ريخته گری، ظروفی به نام تاندیش مذاب را به داخل قالب مسی آب گرد ریخته و سپس در طول مسیر غلطکی با پاشش آب خنک به شمش فولادی منجمد تبدیل می کند.
در نهایت تختال های تولید شده به طول های مورد نظر برش داده می شوند.
تولید شمش با استفاده از کوره قوس الکتریکی
شمشی که از این روش به دست می آید از کیفیت بالاتری نسبت به کوره القایی برخوردار است زیرا در آن یک مرحله آنالیز بیشتر انجام می شود. به همین دلیل است که فولاد کویر کاشان که از روش قوس الکترونیکی برای تولید شمش استفاده می کند، میلگرد گرانتری دارد.
ظرفیت کورهای قوس از یک کیلوگرم تا بیست تن متغیر است. و به دلیل امکان تصفیه مذاب ، شمش های قوس الکترونیکی دارای مزایای زیر است:
امکان تولید شمش کم کربن که کشش و نرمی بیشتری دارد.
نا خالصی های مضر مانند فسفر و گوگرد در شمش قوس الکترونیکی بسیار کم است.
هر محموله آنالیز یک دست تری دارد که بسیار مزیت مهمی است.
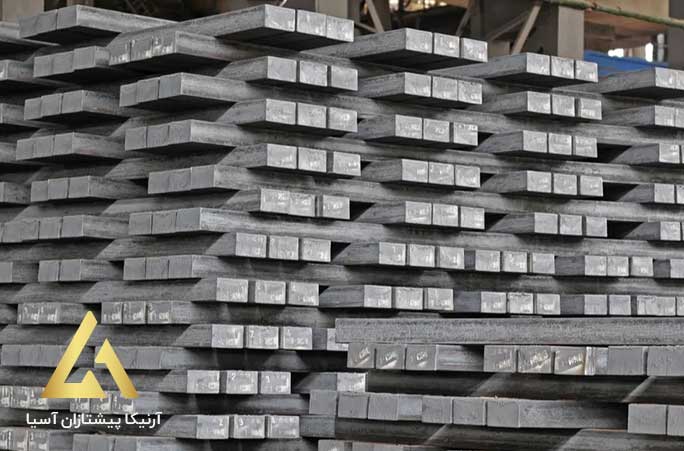
بیلت بلوم اسلب قیمت
معایب تولید شمش با استفاده از کوره القایی:
یکی از مشکلات تولید شمش با این روش این است که به دلیل غلیان، میزان اکسیژن محلول در مذاب زیاد است و این مشکل سبب اکسید شدن محصول نهایی می شود. برای حل این مشکل باید میزان اکسیژن کنترل شود.
یکی دیگر از مشکلات تولید شمش با روش کوره القایی فسفر زدایی و گوگرد زدایی است. این دو عمل در دو شرایط مختلف (یکی با دمای بالای مذاب و دیگری در دمای پایین مذاب) انجام می شوند در نتیجه در صورتی که هم فسفر و هم گوگرد بالا باشد پایین آوردن میزان آن ها سخت می شود.
همه این مشکلات را میتوان با استفاده از کوره تصفیه پاتیلی LF یا LRF یا Ladle Refining Furnace برطرف کرد اما به دلیل هزینه بالای تجهیزات، مصرف نسوز، الکترود، مواد افزودنی و از همه مهمتر میزان مصرف برق بالا ایران از روش فولادسازی با کوره القایی استفاده نمی شود.
از طرفی ماشین های ریخته گری مداومی که در روش تولید فولاد با کوره القایی استفاده می شوند دارای تکنولوژی قدیمی هستند و در نتیجه کیفیت شمش تولید شده نسبت به شمش کوره قوس پایینتر است.
برای دریافت مشاوره و خرید با ما تماس بگیرید.
دیدگاهتان را بنویسید